Oxygen Injection
Anaerobic conditions in force mains are common because oxygen transfer to the wastewater is limited. Oxygen injection is a chemical treatment option that prevents this from happening by providing supplemental oxygen. It is used to prevent the formation of hydrogen sulfide and/or oxidize sulfides that have already formed in the wastewater. The process is like the nitrate addition process, except that dissolved oxygen is the oxidizing agent instead of the nitrate oxygen. The process typically has a higher capital cost than nitrate addition, but operating costs can be less under the right circumstances because liquid oxygen (LOX) is significantly less expensive than nitrates. The oxygen injection process typically involves adding dissolved oxygen into a force main at a pumping station. The oxygen is dissolved into the wastewater under high-pressure using a dissolver where a high driving force exists to dissolve 50 – 200 mg/L of oxygen.
Bacteria in wastewater collection systems will use dissolved oxygen, nitrate, and sulfate as oxygen sources for respiration, in that order of preference. Dissolved oxygen is usually present in fresh wastewater, but is rapidly depleted by biological activity. When dissolved oxygen and nitrates in the wastewater are depleted, the bacteria begin utilizing sulfate for respiration. The byproduct of the sulfate uptake process is dissolved sulfide. The dissolved sulfide combines with hydrogen ions to form hydrogen sulfide.
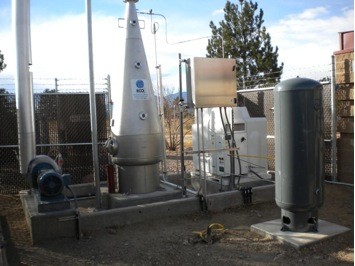
On-Site Oxygen Generation
Oxygen injection works by providing dissolved oxygen for the bacteria, to prevent the bacteria from starting the sulfate reduction process.
Oxygen may be produced on-site or delivered in liquid form and stored in tanks. It may be injected by several different methods, including dissolvers (Speece cone), side-stream U-tube injection or venturi eductors. Pressure swing adsorbers (PSA) and vacuum swing adsorbers (VSA) systems are available to produce 95% pure oxygen on-site and provide on-demand oxygen. PSA/VSA’s allow the Owner to produce oxygen on-site and not have to purchase it from vendors. This equipment concentrates oxygen by compressing the air we breathe and routing it through vessels containing beds of molecular sieve (zeolite). The sieve filters the air and adsorbs the nitrogen at high pressure (60 psig), leaving 90 – 95% pure oxygen exiting the sieve. Before the sieve is completely saturated with nitrogen, the inlet air is switched to a second bed. The first bed is regenerated by desorbing the nitrogen through depressurization and then purging it with oxygen. This cycle is continuously repeated, thus the name “pressure swing adsorption”. VSAs operate in a similar manner but under vacuum instead of pressure.
The sketch shows a typical PSA equipment layout. The system includes an air compressor, filters, air dryer, air receiver tank, oxygen generator vessels containing the sieve, and an oxygen receiver tank. The oxygen in the oxygen receiver tank is then delivered to the wastewater through a sidestream pump and oxygen dissolver. PSA systems are available in many sizes, dependent on oxygen delivery volume requirements.
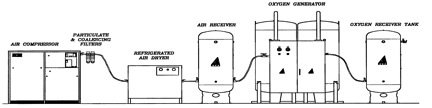
Typical PSA Oxygen Injection Equipment:
Advantages of oxygen injection systems include:
-
- Oxygen has no negative side effects like some of the other chemical addition alternatives
- Systems can be designed to provide residual DO which can have downstream benefits
- Provides odor and corrosion control at air release valves, at discharge structures downstream structures
- No chemical handling or storage if oxygen generated on-site
- Relatively simple operation and maintenance
- Operating costs are typically lower than other chemical addition alternatives
- If oxygen is generated on-site, then owner is not exposed to chemical price increases
Disadvantages include:
- Capital costs are typically higher than other chemical addition alternatives
- Installations with LOX require access by tanker trucks
- Applications are limited to force mains that are under relatively high pressure
- Safety precautions must be designed into the system for the handling of nearly pure oxygen
- On-site generation can be noisy
- On-site generation is energy intensive
Applicable Treatment Processes:
Injection into force mains. Force main must fit into prescribed set of design criteria. For instance, force mains with high discharge pressures work best and the pump station site must have space available for either on-site oxygen generation equipment or space for LOX storage tank and vaporizer.
Typical Design Criteria:
Dosage: Dependent on sulfide loading, oxygen uptake rate and hydraulic detention times.
Major Design Considerations:
- Does the force main operate in acceptable pressure range?
- Is downstream corrosion a consideration?
- Should oxygen be purchased or generated on-site?
- What is more important? Capital costs or operating costs?
- Is manpower available to operate and maintain PSA/VSA?
- Will the site accommodate large oxygen delivery trucks?
- The oxygen should be injected into force mains at a location to allow for adequate mixing and detention time.
- Since oxygen may accelerate combustion, safety precautions must be designed into the system to ensure safe operation.